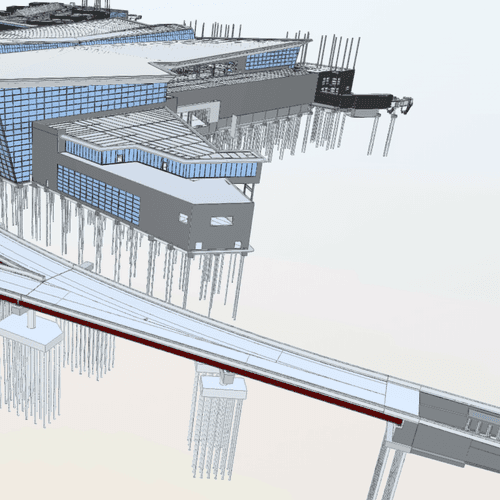
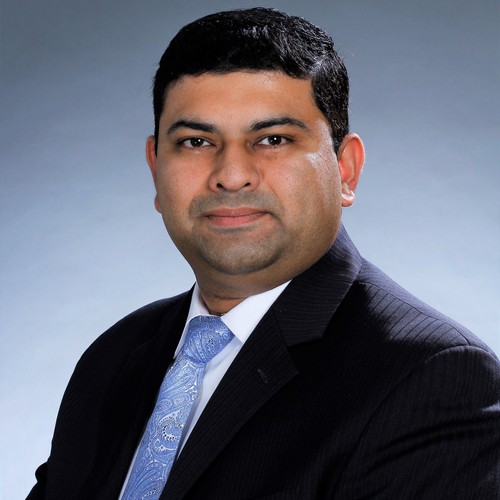
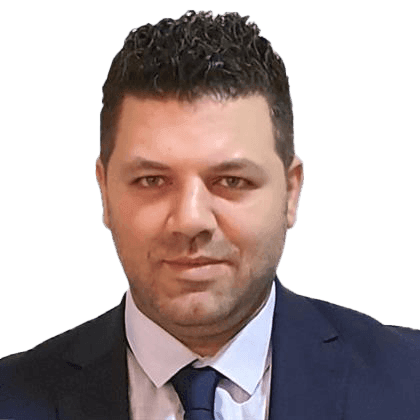
As design engineer for the New Terminal One (NTO) at JFK International Airport (JFK), AECOM has helped our client transform design and construction processes with digital solutions. The Port Authority of New York & New Jersey, in collaboration with JFKTerminalOneCo, LLC, is responsible for this airport redevelopment project.
The NTO will replace the existing Terminal 1 and Terminal 2 while incorporating the former Terminal 3 site. The project involves phased demolition, coordinated construction with ongoing airport operations, and preservation of the existing Air Train. The NTO is the centerpiece of the largest terminal modernization project in the US, adding a new state-of-the-art 23-gate international only facility to serve as a global gateway to the New York metropolitan area.
Tackling early design challenges
AECOM managed the design for the entire airside and landside area for the NTO. Our work included all civil, site, and utility subsurface engineering for the apron as well as departure and arrival roadways. A key challenge of this project was planning, locating, and designing bridges, civil utility networks, and other new JFK NTO infrastructure to coexist with existing utilities and conditions. From the outset of the project, we needed to understand and be able to navigate the underground space between existing Terminals 1 and 4, which is a complex environment, densely populated with existing utilities and characterized by its unique soil type, drainage, vegetation, and topography. The potential for unforeseen conflicts in this environment was compounded by a lack of reliable underground utility information. Our first assignment under the NTO was to develop enough drawing detail of the underground to enable contractors to solicit bids for utilities from utility subcontractors, within two weeks of notice to proceed.
Visualizing the underground
Instead of preparing a set of 2D drawings, we created a computational tool to automatically convert 2D CAD drawings of the existing utilities survey into a 3D environment. Using this automated 3D modelling methodology, we were able to provide a detailed presentation of this complex problem, so that our client and the design and construction team could visualize and understand the existing conditions. AECOM’s engineers created 3D models of the underground space to view and map each of the underground utilities, determine whether they matched the subsurface utility engineering as-built record data or on-site conditions, and then identify which utilities needed to be replaced or moved. Using our automated utility networks generation tool, we were able to automatically place structures such as manholes and catch basins as well as pipes in Revit based on 2D CAD files and highlight any pipes missing information for easy identification. A dynamic link between source drawings and Revit enabled 3D networks to be updated right after changes were applied in the source drawings.
Improving bridge design processes with digital delivery
This early 3D modelling of existing utilities and site conditions kicked-off a broader computational and parametric design initiative for the NTO project. AECOM has successfully pioneered an advanced automated 3D modelling methodology as part of this initiative, seamlessly integrating AutoCAD design data and 3D BIM models in Revit. On the new departure bridge project, potential conflicts with existing structures and utilities alongside operational, safety, and regulatory requirements posed many challenges. Our advanced 3D modelling methodology provided significant enhancements in efficiency and consistency in bridge design processes. Using a federated project information model, we carefully and effectively managed complex interfaces among the different disciplines of the project.
Key features of our digital delivery
- Develop an automated 3D modelling methodology: We integrated AutoCAD and Revit to automate 3D modelling and streamlined tasks and processes through computational design techniques.
- Manage data: We implemented a comprehensive data management strategy, ensured a smooth workflow, and informed users about file positions in the process.
- Automate tasks and projects: We used visual programming software for automation and implemented automation at three data levels — overall process, operations, and parametric components.
- Collaborate and share knowledge: We facilitated collaboration and knowledge sharing between teams and ensured transferability to other projects.
- Scale-up and deploy: We explored scaling strategies for wider implementation and developed guidelines for future Port Authority project use.
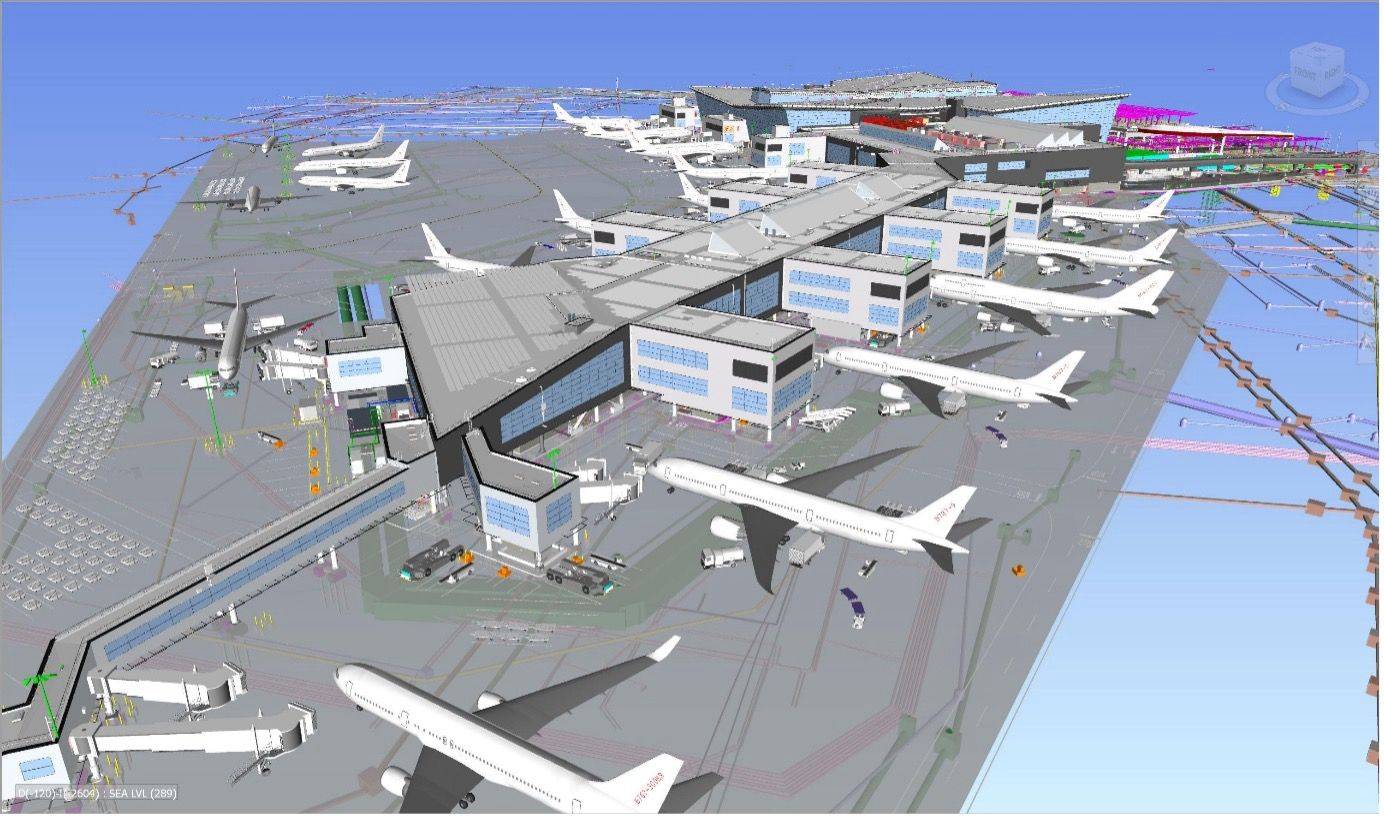
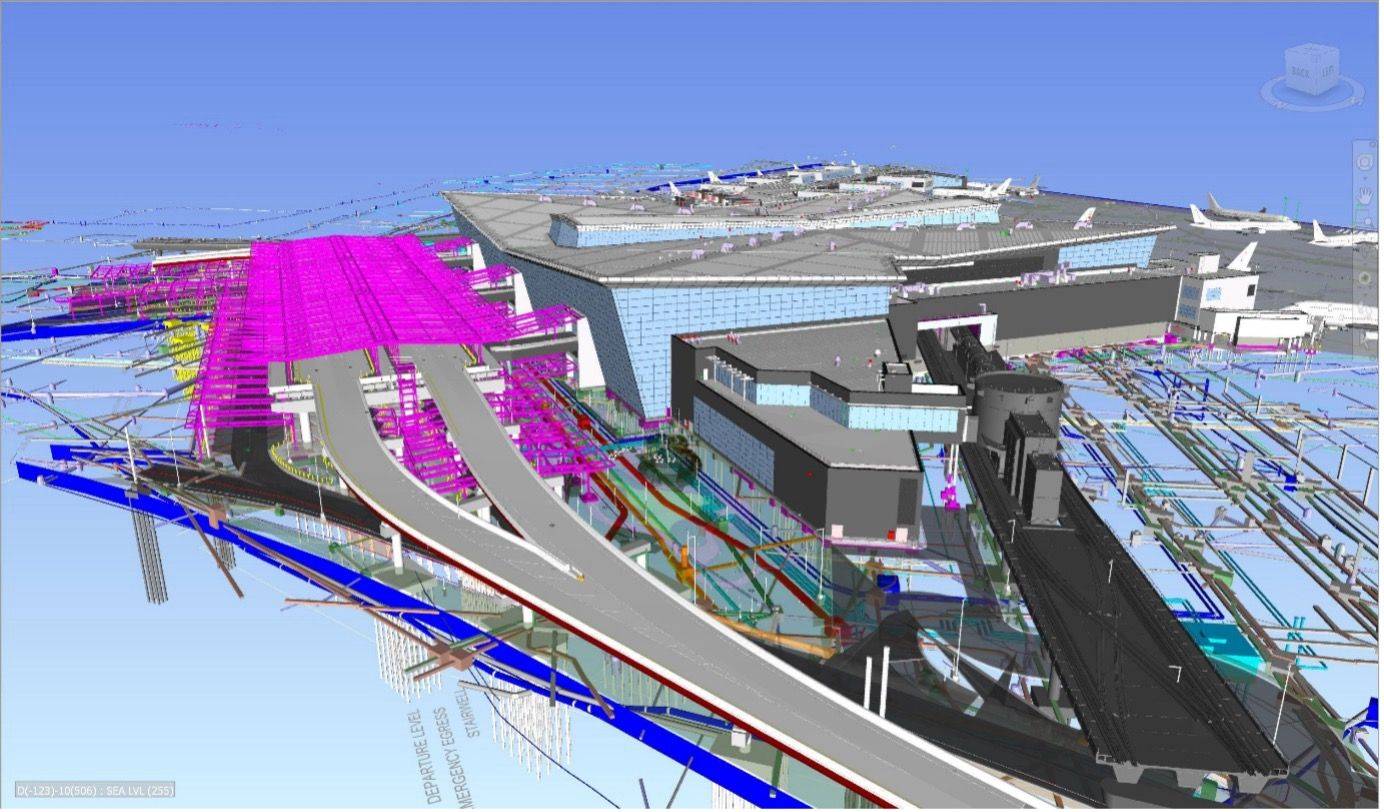
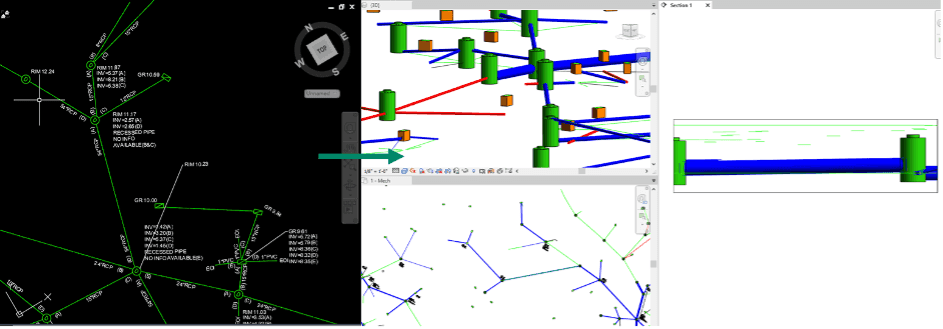
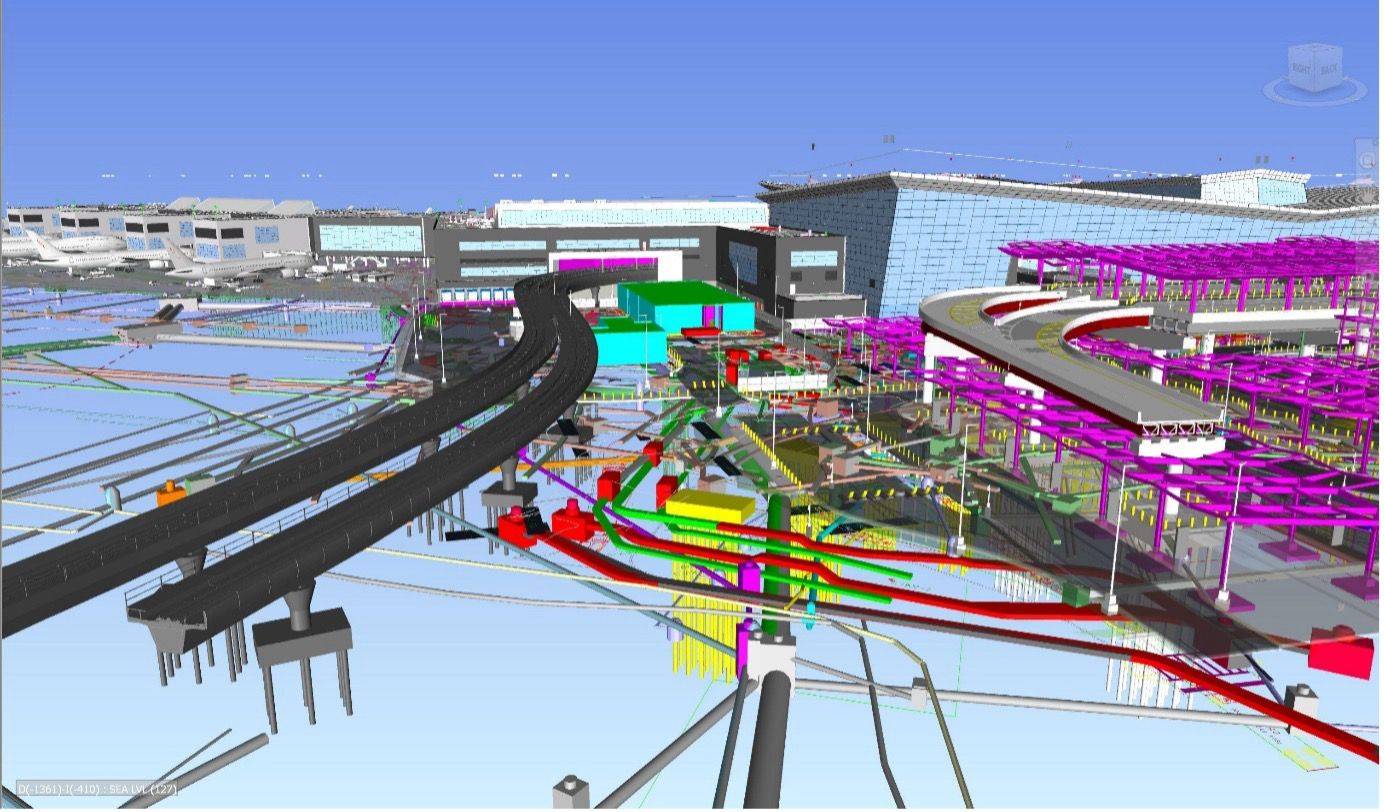