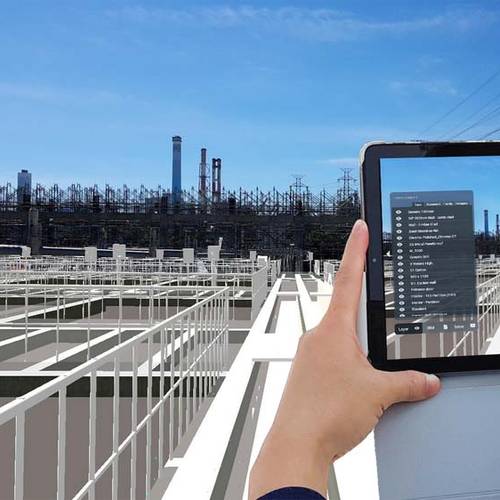
This onsite augmented reality-based construction management tool integrates BIM and augmented reality (AR) technology to project 3D models onto the physical environment at 1:1 scale.
Global investments in BIM have been rising rapidly in recent years, and the market scale of BIM-related software and services is estimated to reach approximately $11.7 billion by 2022, according to Allied Market Research. However, only 29 percent of BIM projects passed the BIM data to management and operation work, and only 49 percent of projects used the BIM 3D model from the very start to the very end of a project.
The considerable gap between the data usage in virtual design work and onsite construction, inspired the creation of our new Augmented Reality (AR) Spatial Visualizer solution. By offering engineering teams access to a digital 3D BIM model on job sites, we can ultimately reduce the amount of conventional paper-based onsite management work.
Our new digital tool, AR Spatial Visualizer (ARSV), integrates BIM and AR technology, and is capable of projecting 3D models onto the physical environment at 1:1 scale. This product extends the usability of existing digital assets and benefits the whole construction life cycle with smart and cloud collaboration.
In most cases, field staff struggle with hundreds of paper-based documents for regular inspection work. With ARSV, the onsite team can easily access a variety of BIM data (architecture, structures and MEP) onsite and identify hidden problems earlier, achieving higher efficiency and better accuracy of project communication, QAQC or even maintenance.
The ARSV includes three major benefits:
- Unlock the value of existing 3D assets and data: The ARSV empowers mobile devices to access project 3D models onsite, increasing the usability of the model and BIM data in the whole construction life cycle.
- Uncover hidden issues with higher accuracy: Overlaying a 1:1 digital model onto the physical space enables field staff to check MEP equipment and structures behind walls and ceilings. This helps to reduce the risk of rework and delays as well as site hazards.
- Smarter coordination with less onsite effort: Creating issue reports on mobile devices onsite and synchronizing those findings to the cloud database allows other team members to check and fix remotely from the office or even their own house. This reduces the need for additional team members to be on site and improves efficiency.